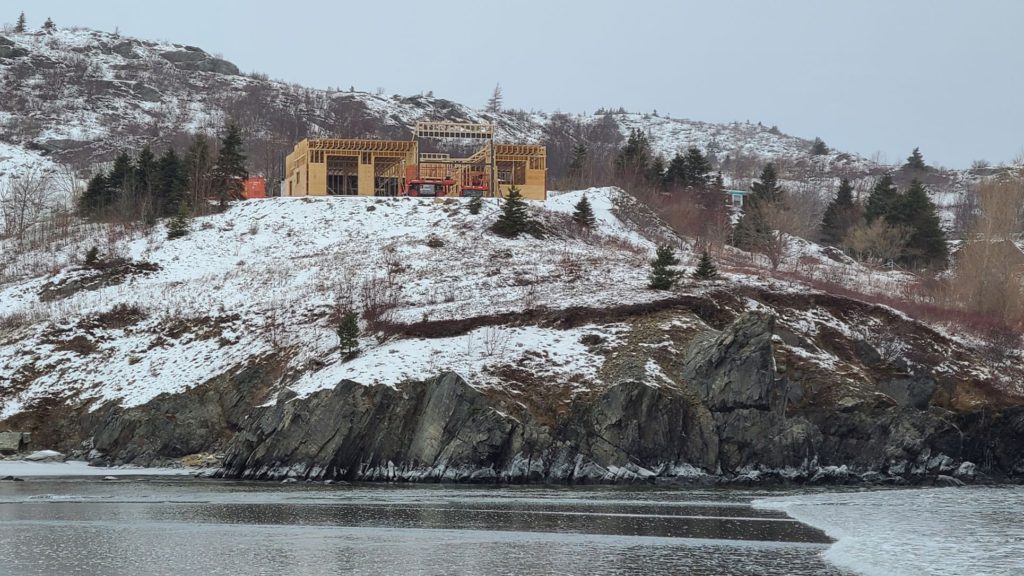
As the form of the house starts to appear, it will be apparent that there are only three basic blocks. There is a low roof section on the east and west sides and a higher roof section that is central. The two low roof portions essentially run the full depth of the house, and the central (high) section runs from the south wall – but only as far back as the steel framed (buried) area on the north side. The high roof area will hopefully help define the main living space and add a bit of drama and interest overall. It will also provide an opportunity for three clerestory windows that will bring natural light into the core of the home.
The framing is progressing based on erecting the two low areas first. This will allow for a secure and logical platform to frame the upper section (walls that extend from the low roofs to enclose the sides of the high roof area). Therefore, the aim here is to have all the necessary interior and exterior wall framing completed to facilitate the installation of the roof trusses over the low areas.
Construction is a lot like stand-up comedy. So much depends on timing.
The flat chord roof trusses have been fabricated in Mount Pearl by Atlas Structural Systems. They arrive at site on a forty-foot trailer and occupy every inch of the float. The crew have already determined that getting the semi-tractor and trailer up the driveway to the site is pretty much impossible without knocking down some of the neighbouring houses, so a crane is also on site to perform a multiple lift exercise over the gates and trees and up the driveway while ensuring that all utility lines remain intact. We are indeed fortunate that NL Power’s poles are on the opposite side of the street (out of harm’s way).
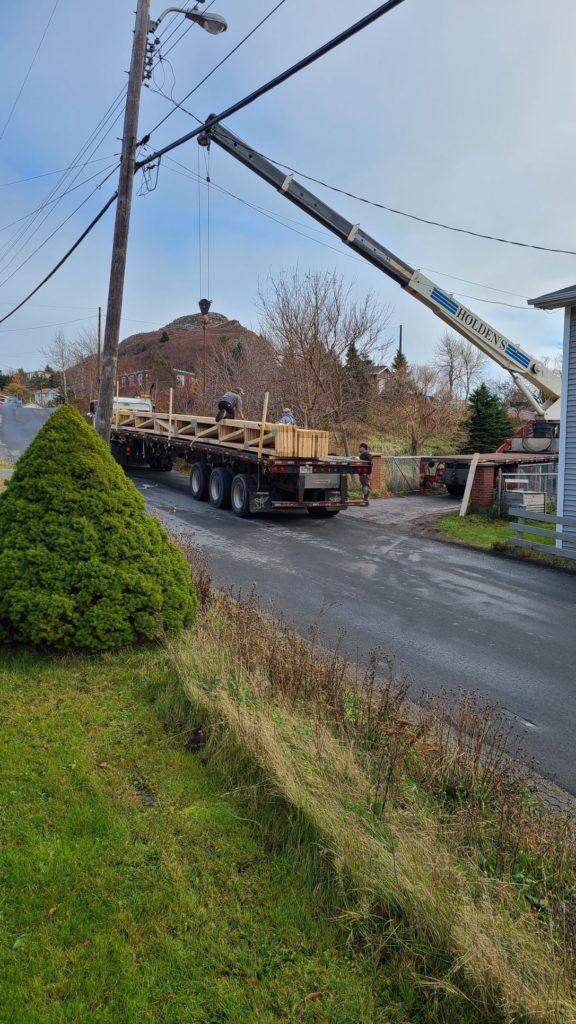

The contractor’s crew and the crane operator somehow manage to get the roof trusses off the float and up the driveway using a degree of ingenuity that cannot not be found in Toronto. By the end of the day, every bit of lay-down space near the newbuild is littered with flat chord behemoths.
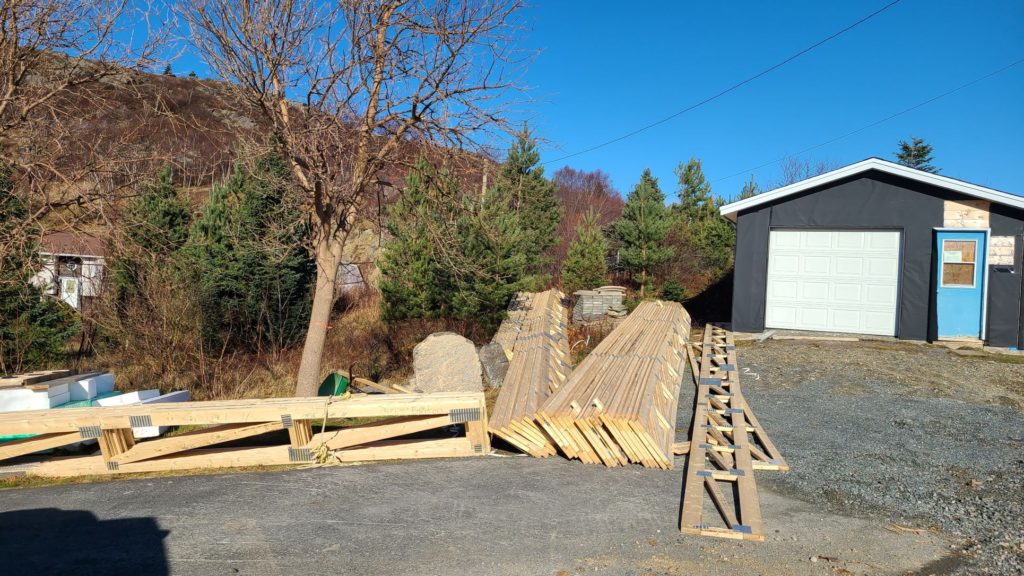
The contractor’s crew complete some additional framing as we wait for a day with no wind. That statement in and of itself is comedic. The forecast offers a window, and on the given day a boom truck appears. The intent is to get all the trusses installed on the two low roofs before nightfall. Mission accomplished as the process goes like clockwork. As the trusses are placed they are temporarily ganged together to preserve their alignment and plumbness until the ¾” tongue & groove plywood decking goes on.
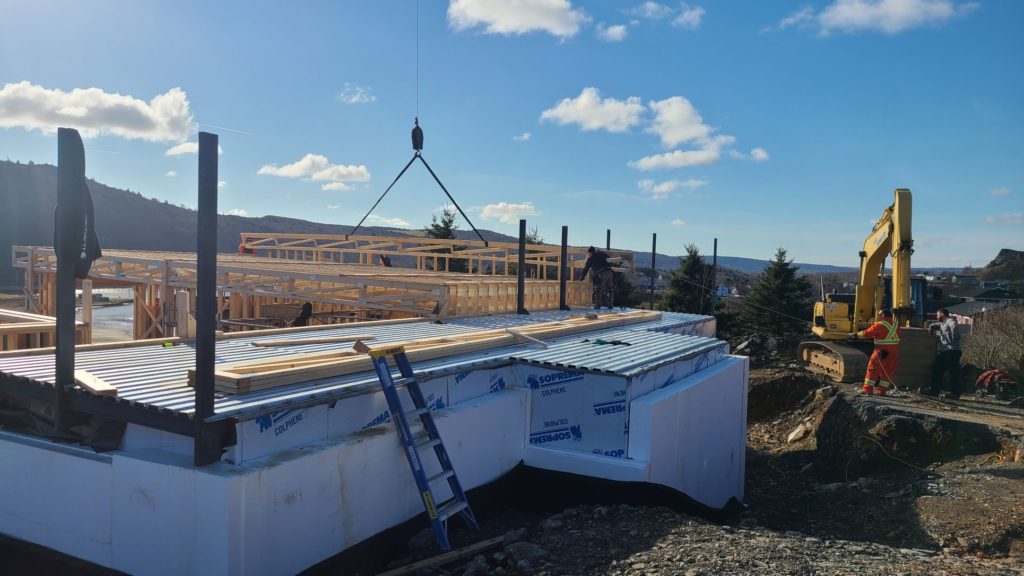

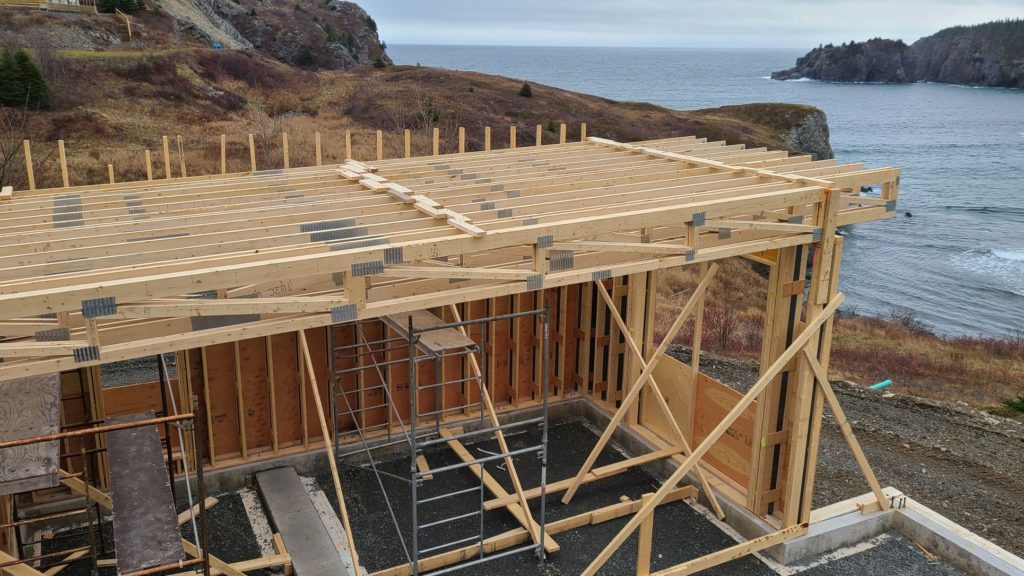
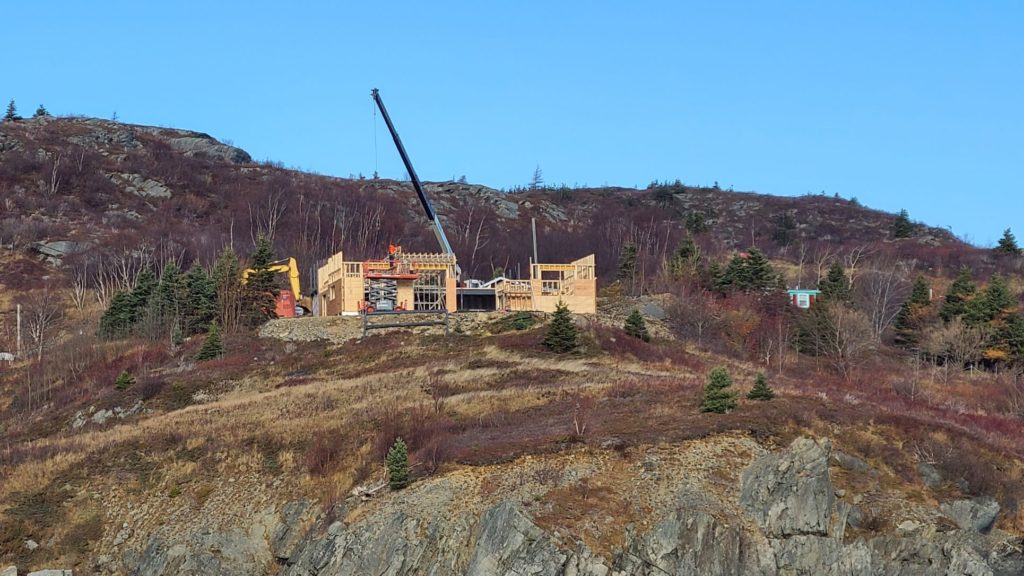
The trusses all cantilever over the south face of the house to provide a shading canopy which is essential to prevent overheating in the summer. The depth of the cantilever has been designed to shade the windows and doors from the sun while its inclination is highest (the days preceding and following the summer solstice). In fact, energy modeling of the design has shown that the risk of overheating is actually greater during the spring and autumn equinox when the sun is at a lower inclination! Of course, the cantilever will not have a shading effect during the winter when the sun’s angle is lowest.
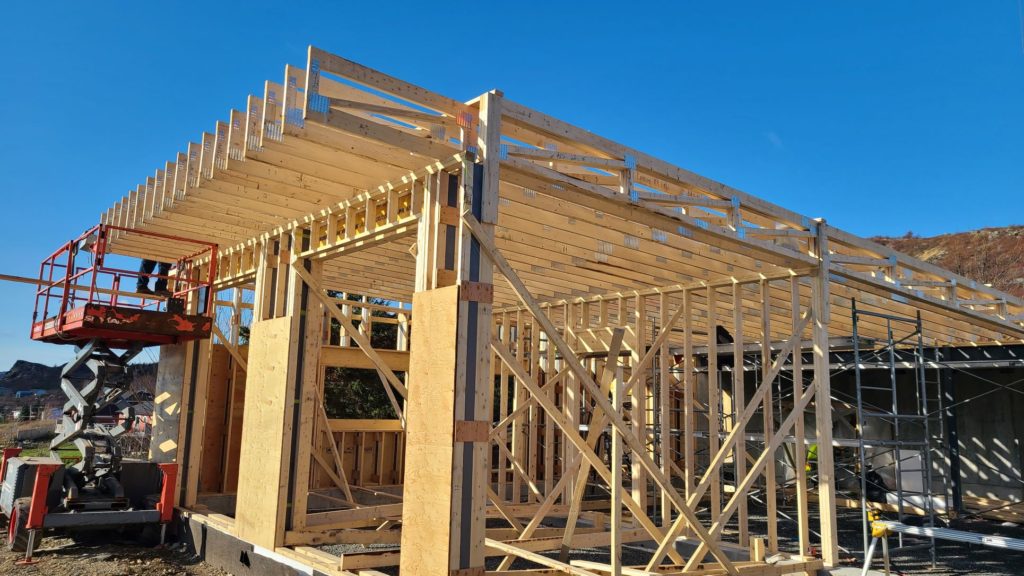
The following day, decking over the two low roofs begins. The T&G plywood can be a bit of a headache at times because the joints must be accurately aligned and each sheet pounded into place. But these joints are far superior to butt edges from a structural perspective and given that as I am writing this the wind is gusting to 100 km/hour, I can take solace in any additional roof strength.

I would also hasten to point out that one member of the crew has been assigned the task of securing a hurricane clip at each and every location where trusses are bearing on the framing top plates. The photo below illustrates what a hurricane clip looks like (not from this project) but does not emphasize enough why anyone in their right mind would build without using them.
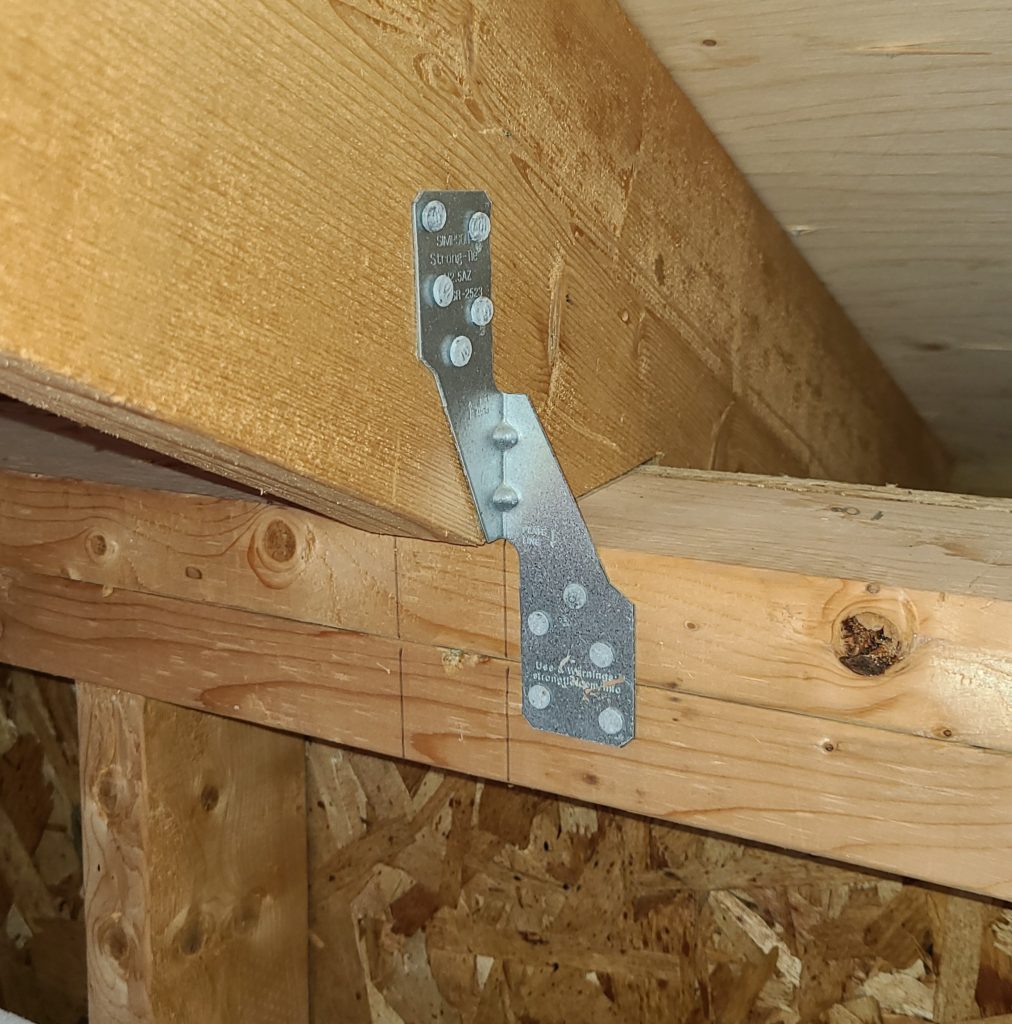
One other note of interest that you may have already gathered from the pictures embedded with this post is that the steel frame that supports the glazed doors and transom windows in the main living space has been erected. You now get a sense of that incredible view which prompted this adventure.
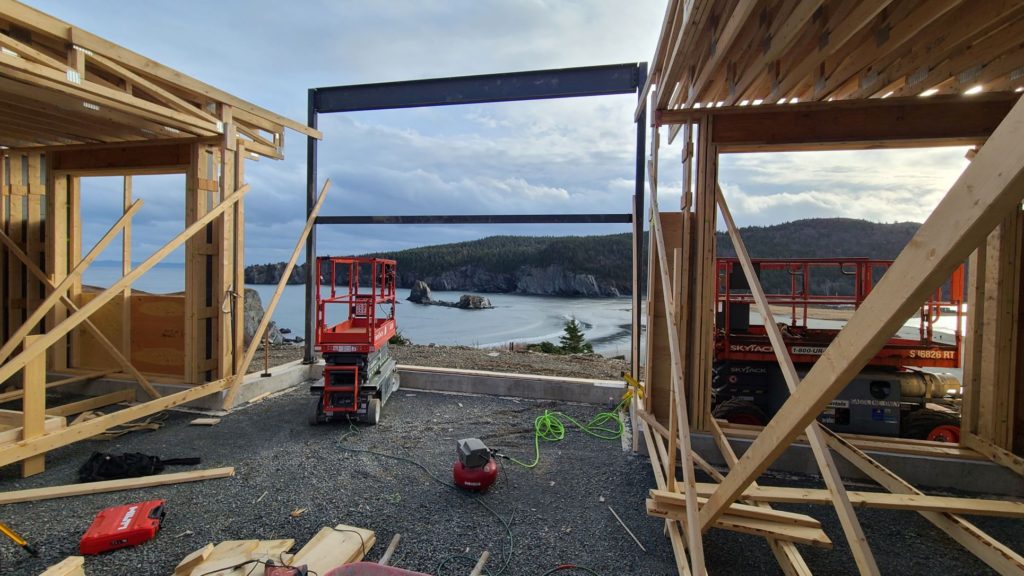
We postponed this installation (even though the frame has been lying around since the steel guys were here – indicated in some previous pictures). We did not want to tempt the wind gods by having this as a freestanding item for a couple of months, but now that the two wing walls are in place, along with roof structure at either side, the whole assembly can now come together to produce a welcome stabilizing effect.
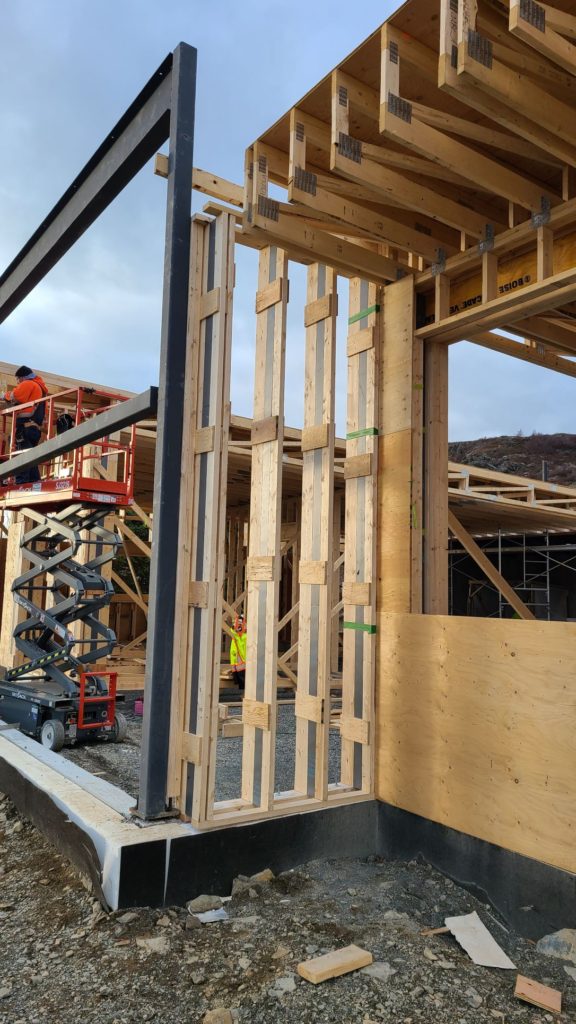

The steel frame gets prepared to accept the trusses of the high roof. You can see this in the picture above right. As part of this prep work, the knee-wall at the north (terminating at the steel framed construction) is built to accept the high truss at the opposite end together with an internal loadbearing wall that will support the trusses at mid-span.

I will update you all, dear readers, with another post regarding the installation of the high roof trusses. For now however, it will simply have to wait until this cursed wind stops blowing.
Keep it coming James!! Even though I may not fully graspo every detail I understand the basics and it’s a pleasure to watch to progress. “Give ‘er my son!”
I can confirm from my own observations (in a Passive House) that we very rarely have “overheating events” . In the passive house world an event is considered to be above 25 degC for more than 10% of total annual hours. I can say that we never reached this during summer. typically it happens in the shoulder seasons. As you said, overhangs help, but once exterior temperatures start rising, you’re at the mercy of physics. Based on the PHPP model, we chose to go without air conditioning. The model estimated that we wouldn’t need it and the cooling load was tiny. Unfortunately, PHPP does not model humidity into the energy model. WUFI does I believe. Unfortunately the choice to go without air conditioning turned into an interesting human comfort experiment! It also illustrated the variability between inhabitants (me and my wife). As exterior humidity increases, interior will also with ventilation. 25 deg C in the house on a sunny day is not that uncomfortable in the spring when the relative humidity is 40%. When it’s 26 degC and 65% humidity, its quite uncomfortable and stuff for some…not for others. It seems my tolerance is quite different than my wife. Once it hits 70% I start puffing and blowing. We realized quite quickly after 1 year that the latent load was an issue. Humidity would need some mechanicals. We added a mini split and set it on dehumidify mostly all summer. It runs at half the cooling power, and the purpose is just to decrease the latent load. there is some sensible cooling effect but the major effect on comfort level is due to decrease in humidity.
Hello David! With the huge expanse of south-facing glazing that we have there is no doubt that were it not for the shading characteristics of the cantilevered roof, we would have a significant overheating potential. That amount of glass has far less to do with energy than it does with aesthetics. Your humidity argument is valid. That is why in our design the incorporation of high quality (Big Ass) fans is integral to the design (as opposed to dehumidification). Rapid air movement has a desirous psychrometric effect in high humidity situations. In addition, we will have hydronic slab conditioning by means of a heat pump. Again, this is a life choice – not an energy one. We will have the option to cool our slab-on-grade in the summer. This will be a bit of a balancing act however, because of the potential for surface condensation. We’ll see how it goes!
Jim,
Your new home is a very interesting project showing how much detail and planning that you have put into this structure. I’m looking forward to seeing each progress report.
As for hope of the winds abating 🙈. Good luck. Our Holyrood home is 170 feet above sea level and approximately 750 feet from the shore line and my weather station hasn’t got much of a break from the wind in weeks.