
We have a massive hole in the ground. I use the term “ground” loosely.
The footprint is checked using a theodolite and stakes are driven to mark the footing layout, otherwise a spot of surveyor’s paint is sprayed onto the bald rock. For the uninitiated, footings are used to help spread the dead load of the entire house (together with live loads – people, furniture, snow) over a wider area of earth. We actually have portions of the footprint that are not on rock, so we will abide by construction norms and locate footings beneath all the exterior walls.
Strip footing sizes vary depending on soil locations, but are typically about 10 inches deep and two feet wide. Your structural engineer will assist you on sizing and determine whether or not reinforcing steel (rebar) is required. Structural engineering services were retained for this design as it is, shall we say, anything but normal. (A phrase often employed by friends and acquaintances to describe myself.)
One thing I would like to point out has to do with preventing any movement between the footing and the foundation wall which is cast upon it – movement caused by backfill pressure and sometimes frost heave. In the centre of the footing the contractor will float in a 2×4 when the concrete has been placed. This is removed when the formwork is stripped (usually the following day) to form a continuous channel in the top of the footing. It’s called a “key”. If your contractor suggests the key is not required, you have the wrong contractor. Alternatively, vertical rebars can be installed in the fresh concrete. They achieve the same. An overzealous structural engineer may request both, especially in a retaining wall situation.
I have such an engineer.
Constructing the formwork for strip footings is usually accomplished by the contractor’s own forces using standard dimensional lumber held in place with wooden stakes or rebar and supported across the top at four foot intervals with 2x4s. Easy peasy.
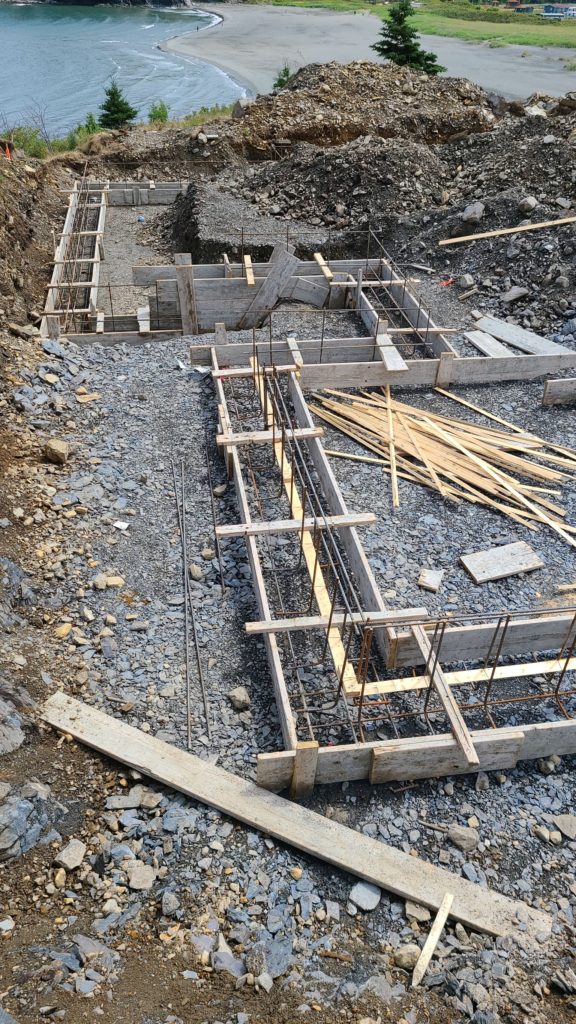
In the picture below, you can see where the overall foundation will be stepped. As you may recall, this was to avoid excavating more rock (impacting schedule and budget). Also, note the 2×4 that will form the key.
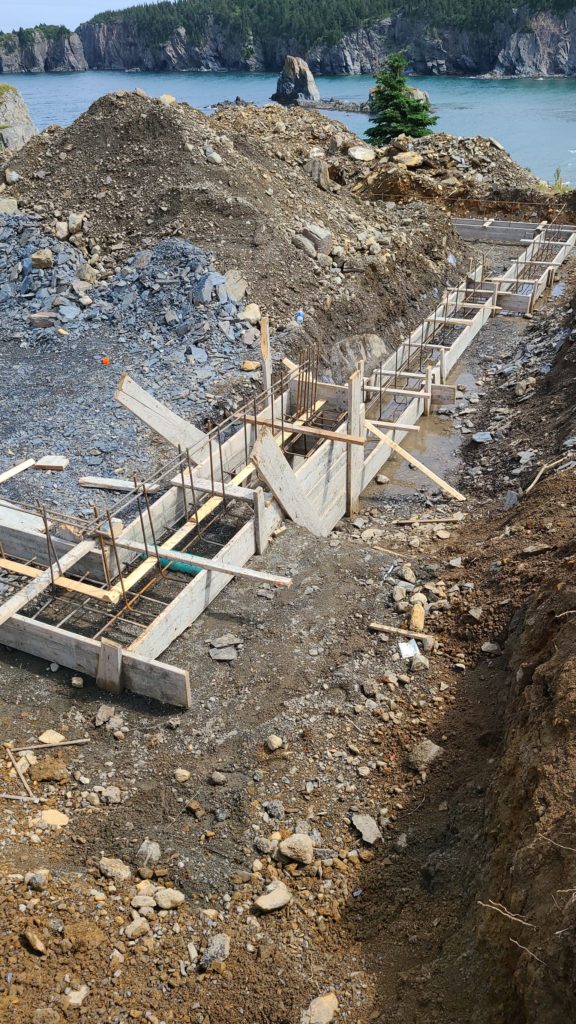
Footings are also required for interior columns as can be seen in the next picture.

Normally, a concrete truck can access around the site, in which case the concrete chute will be directed into the formwork with the truck stopping / starting around the perimeter. Often, in less accessible places, the concrete is physically carted from the truck to the footing location via wheelbarrow. I have done this many times. It’s no fun. And the wheel will bump to a stop on a grain of sand requiring herculean strength (or drugs) to regain momentum.
So we’ve brought in a pumper. And she’s a beauty. Brand new. Complete with splendid chrome bumpers. It sets up like a huge lobster with an articulating snorkel of incredible reach. The concrete trucks back up to the pumper and simply divulge the concrete content into its hopper from whence it can be pumped to anywhere within about forty metres.

The neighbour’s reaction is one of shock and awe.
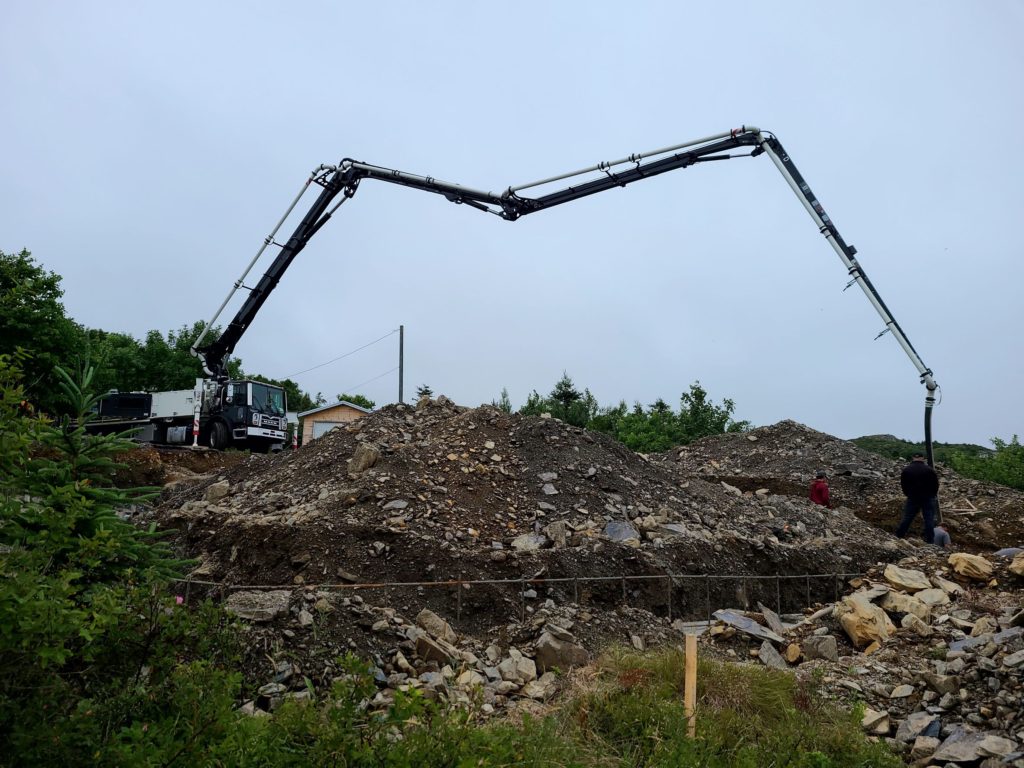
Finally, as mentioned in the previous installment on this blog, a decision was made not to place the footings on insulation. We were uncomfortable with this Passive House guideline based on climate, schedule and cost. This will be one of the many decisions where such factors are weighed against payback. However, I won’t hesitate to note that today’s polystyrene insulations are more than up to the task in terms of compressive strength, especially extruded products and Type 3 expanded foams. More on the latter product in my next post.
Great photos, I now have the smell of fresh concrete in my head
Very informative Jim. I’m in the process as of now building a slab on grade home in Topsail. I look forward to your posts,
Thanks for sharing this. I too will be looking at the daunting prospect of building a house (first and last) for retirement in a few years, on land already purchased from the family estate sale. I look forward to learning since house construction is completely outside my wheelhouse.
– Lloyd
Well I hope this is helpful Lloyd!