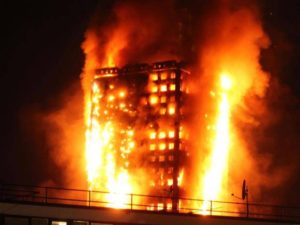
When I started to practice architecture in the late 70’s and early 80’s, I bemoaned the fact that the choice of exterior finish materials or building cladding was extremely limited. Cast-in-place concrete facades pretty much died out with Art Deco (although we are left a handful of marvelous buildings from that time).
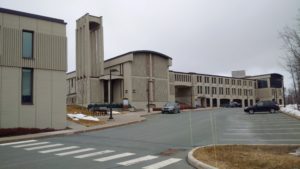
Precast concrete panels as a façade finish were popular in the 50’s and 60’s because Lundrigans out of Corner Brook (a favorite of the Smallwood government) had made this their specialty. They were very competent, but precast was lost as an option in Newfoundland as the Smallwood era came to a close and Lundrigan’s became a victim of political history.
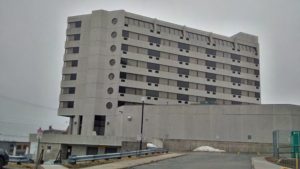
Trinity Brick was still being manufactured in the 1980s. It was a superlative product in terms of its robustness in our climate. Manufactured in three shades of brown, it was the cladding product of choice, especially when carrying on the mercantile architectural styles of the capital city. But brick and block systems became largely unaffordable for most buildings, and Trinity Brick became a casualty. All of our brick is now imported, mostly from the Maritimes.
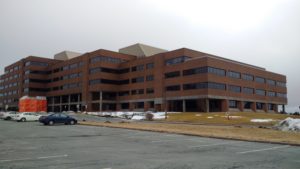
Metal siding began to come into its own as the cheap alternative. Crinkly tin as some like to call it. A favorite of the provincial government, especially for school construction, because it was, shall we say for want of a better descriptor, economical.

Wood (clapboard and various derivatives) was always a fallback, but this was an unpopular choice because it had to be painted – and the stain technologies that we have today were still in their infancy.
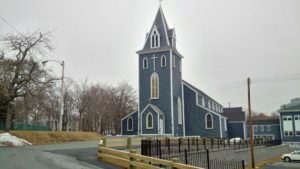
Glass, or curtainwall as we architects like to call it, was excruciatingly expensive. Still is – but technological advancements have made this one of the most reliable cladding systems, so it has gained popularity almost in lock step with the disdain afforded it by the heritage and environmental types. Fair criticism.

So back in the late 80’s, this young architect marveled at a new product that was appearing in all the latest magazines and glossy architectural journals: a sandwich product called composite aluminum that, despite being incredibly thin and light, could be formed into perfect geometric shapes without distortion or impairment. It was about that time that the Danny Williams Avalon Cablevision empire began to blossom, and the company was looking to expand on a property it had acquired (out in the wilds) on Kenmount Road. It was a brown brick box that housed the company’s “head end” – all the kit that at the time brought life to our televisions.
Danny was always a forward thinking guy. (No kidding.) So I pitched this new material to him. It was a bit futuristic, like Avalon Cablevision, so he suggested we try some of it – not too much – all a bit of a risk you know. So my buddy Dick at Trico (the best metals guy this province has ever seen) says “Let’s have at it”.
Dick predicted this stuff was going to take off like wildfire. He was right – figuratively and literally.
So the building that is now Rogers was the first installation of aluminum composite panel in the province. It would be placed above the strip windows and curved at the intersection. It would also feature a coloured reveal. Have a look next time you’re headed out to Kelsey Drive for your Home Depot fix. It’s a piece of architectural history really. Yep. All that and a bag of chips.

So the product evolved rapidly across North America, and two or three manufacturers (Reynolds among them) really started flogging it.
At the time my boss was Reg Whitten – an extremely competent engineer, and cautious, especially when it came to fire and life safety. As aluminum composite evolved, so did a host of new plastic insulations, particularly expanded and extruded polystyrenes and polyisocyanurate. Reg was concerned about how building codes were going to deal with these products. Plastic burns very well, and in so doing, gives off deadly toxic gasses. He would not hear of using such products on buildings exceeding three stories (incidentally, a code cut-off point for many life safety items) or on a building designed to house non-ambulatory persons (hospital or nursing home).
Scale and context are more than relevant when considering the use of aluminum composite.
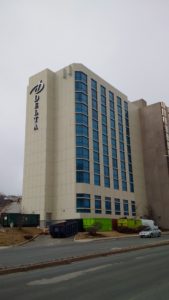
The National Building Code at some point along the way set significant restrictions on combustible insulations and also introduced a test requirement for cladding systems. It was CAN/ULC-S134 Standard Method of Fire Test of Exterior Wall Assemblies. It was my first indication that something was up with aluminum composite panels.
Typically 3 mm in total thickness, aluminum composite panel (ACP) consists of two sheets of aluminum sandwiched together with a polyethylene core. The product is brilliant in many ways. It can be formed into curves, and can be routed on site with rudimentary tools and equipment to form perfect corners. Its fastening method can be completely concealed. It can be anodized or painted. It can even be screened to look like wood or stone (not that you’d want to use something like that – just too tacky). But it’s a relatively economical cladding choice, especially for retrofits.
As ACP demand grew, manufacturers from all over the world mastered the product concept. There were dozens. Perhaps hundreds. But at best reckoning, only about three manufacturers had a product that passed CAN/ULC-S134. All these manufacturers also made lesser grades to compete with eastern knock-offs.
It was a curiosity. I could not understand why all these inferior versions were on the market. How was it that the fire rating was not an issue elsewhere? Was the restrictive code requirement only enforced in Canada? Were all the authorities having jurisdiction cognizant of CAN/ULC-S134 and were they enforcing it?
I often considered these questions but they never really hit home until the Grenfell Tower Fire.
A great history lesson in this post – really enjoyed it! And I would love to learn more about the St. Bride’s College building – perhaps a future post!